
Specifying the Right Floor—Part III
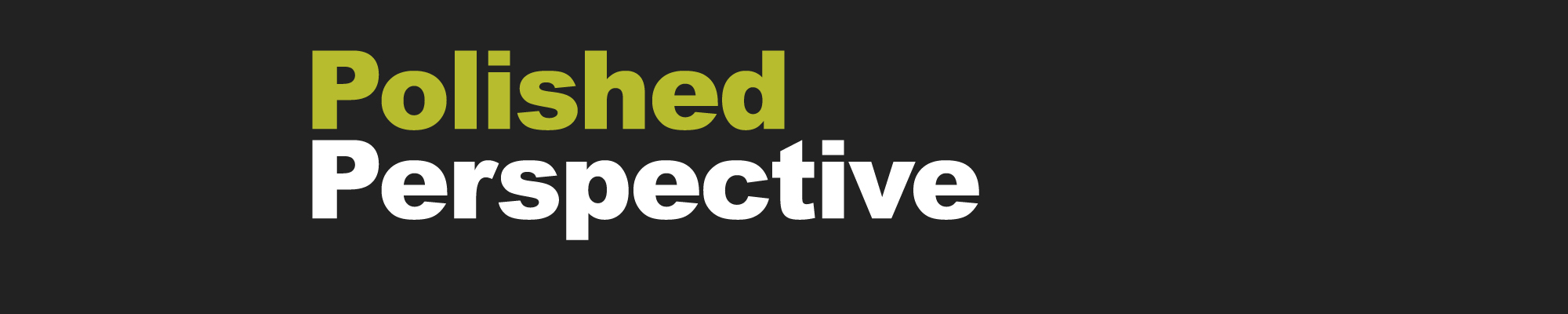
POLISHED PERSPECTIVE
The Architect’s Viewpoint: Specifying the Right Floor—Part III
By Andy Bowman
Preparation of the Concrete Surface
As the industrial coatings industry has evolved, the importance of surface preparation has grown in importance. Just as the success of a paint job depends on surface preparation, so too does the success of concrete protection. Because of the way concrete cures, two conditions must be met before any coating can achieve a good bond with a concrete floor.
- The surface must be clean of dirt, chemicals and other contaminants.
- The surface must be given a mechanical etch or profile.
Surface profile can be described as the miniature ridges and valleys that give concrete the “tooth” or “profile” required to form a successful bond. Without a good profile, the chances of floor blistering or chipped coatings increase significantly, and the life expectancy of the floor is reduced.
Over the years, several methods have been developed to clean and profile concrete:
- Cleaning and etching
- Abrasive blasting
- Scabblers
- Scarifying
- Shot blasting
- Diamond Grinding
- High-pressure water jetting
Cleaning and Etching
Acid Etching—Of all the cleaning and profiling methods, acid etching produces the lowest profile and is useful when the floor is going to be coated with a very thin system such as a clear urethane. The profile is similar to the roughness of 200-grain sandpaper. There is a widespread misconception that acid etching is the only process necessary to clean and profile concrete, but acid doesn’t remove coatings, dirt, oil, grease or fat from concrete surfaces. Thus, other surface preparation procedures are needed in cases where cleaning is required. All contamination must be removed prior to the application of acid to create a uniform profile. Hydrochloric acid (previously referred to as muriatic acid) is most commonly used for etching, but citric acid and some others can also be used. An average job of acid etching requires three or four workers.
Chemical Stripping—This method removes concrete coatings. If coatings on the concrete are layered or thick, more than one application of the chemical stripper may be needed to remove the coatings completely. The process of chemical stripping is relatively labor intensive, and produces a substantial chemical residue that must be disposed of properly.
Detergent Cleaning—Detergents remove dirt, oil, grease and fat from the surface of concrete flooring. Detergents are most commonly applied with powered floor scrubbing machines. The use of concentrated solutions results in higher detergent consumption but insures the complete removal of grease and oil, unless they have penetrated down into the concrete.
Abrasive Blasting—Conventional abrasive blasting with sand is the dirtiest method of cleaning concrete floors because of the large volume of dust that gets into the air. Equipment must be completely masked and abrasive blasting typically requires a cleanup afterward. At the same time, however, abrasive blasting is very effective in creating a well profiled, uniform and clean surface to which concrete coverings can adhere. Wet abrasive blasting may be used to suppress dust. Abrasive blasting can be used to lightly abrade the surface, or it can remove the top surface of the concrete altogether.
Scabblers—Air-powered units that use a number of small pneumatic hammers to pulverize the surface, thus providing an extremely rough profile for toppings and overlayments. They are very effective at breaking up delaminated toppings and, in some cases, overtrowelled or crusty concrete surfaces. Dust generated by the scabbler can be controlled by applying water to the surface; however, clean up of the surface must be thorough. Any pulverized material or sludge left on the surface can cause a bonding failure.
Scarifying—To scarify a surface means to scratch it. Scarifying machines scratch the surface of concrete to remove dirt, coatings, grease and sealers. Scarification is done with a rotating drum, which has hardened cutters that scratch or abrade the concrete until all surface contamination is removed and sound concrete is exposed. Scarifying can achieve a profile ranging from 60 grain sandpaper to 0.125-inch grooves.
Shot Blasting—Similar to abrasive blasting. However, the abrasive used is steel shot, which is mechanically propelled by a rotating blast wheel instead of by compressed air. The blasting process is contained within a housing and the abrasive is recycled continuously. The pulverized concrete and contaminants are collected by dust collector units, thus providing the advantages of an abrasive-blasted surface without the massive cleanup required with open air blasting. Shot blasting can be controlled through a wide range of profiles, from light brush blasting to removal of 0.25 inches of the top surface. Control is maintained by varying the size of the abrasive, the travel speed of the unit and the amount of abrasive thrown. All this illustrates the relationship of the different sizes of abrasive to the profile delivered.
Shot blasting is primarily known as an all-purpose, one-step cleaning and profiling method for concrete floors. It can efficiently clean materials such as dirt, grime, old coatings and embedded chemical contaminants. It also can be used in plants without the need for protecting sensitive equipment. Where there are not massive amounts of grease and oil on the floor, the recycled steel shot is cleaned sufficiently by the machine’s air-wash separator so that the grease and oil are not redeposited on the surface. During recycling, dust from the concrete acts as a drying agent on the oil and grease and helps clean the abrasive. The shot-blasted surface is uniformly clean and profiled, readily accepting all coatings applied to it. In effect, a thin layer of the surface is blasted away, leaving essentially virgin concrete that will absorb the first coat of most systems.
The bond strength of coatings applied to shot-blasted surfaces has been measured and found to be equal to the tensile strength of the concrete to which it was applied. Labor requirements for the shot blasting units are very low, thus providing lower overall surface preparation costs. Cleanup following the blasting process usually consists of sweeping the area with a magnetic broom to pick up any loose abrasive that might have escaped the blasting unit. Shot blasting is ideally suited for preparing surfaces for epoxy toppings and most coatings, but the cleaning paths can show through clear urethanes due to the graining effect and the overlap of succeeding passes on the concrete surface. This graining appearance, similar to what is seen when mowing grass, is produced by most mechanical surface preparation methods.
High Pressure Water Jetting—This is a recent innovation for cleaning and preparing industrial flooring for coating. Water jetting units generally use an engine-driven, piston pump to develop pressures of 15,000 to 25,000 psi. The blasting is accomplished by hand-held wands or lances, and by units that have two nozzles attached to a rotating bar. The rotary unit, which looks something like a lawn mower, is used to create a more uniform surface finish. Water jetting has the advantage of controlling dust in the cleaning process. While it can create a profile, it is difficult to control the profile because the high-pressure water is very aggressive. In 1984, ultra-high pressure units were introduced for demolishing bridge decks and parking garages. These units are used in place of jackhammers for removing delaminated concrete and exposing reinforcing bars in slabs.
Installation of the Flooring System
Once the flooring surface has been prepared to receive the coating or topping, the installation should be relatively simple and straightforward. However, it is important to recognize the following considerations.
Joints and Cracks
Do not coat expansion/isolation joints. Fill with the appropriate joint material, flexible or semi-rigid, after installation of the coating. Saw cuts, cracks or control joints can be filled and coated over in a temperature controlled environment.
Temperature
100% solids epoxies are dramatically influenced by temperature. Working time, cure time, viscosity (mixing & flow), air release, surface tension and pigment float will all be affected. These products work best at 70-85 degrees Fahrenheit in a combination of surface, product and air temperature. Outside of this range care will need to be taken to ensure success. For example, a 15-degree change in resin temperature (from 70 to 55) will more than double the viscosity of the product. The resin will still cure at 55, but mixing, flow, air release and pigment float will all be negatively impacted. A product temperature of 70 is ideal, but if placed on a 45-degree substrate it will not flow, release air or cure as hoped.
Dew Point
The temperature at which moisture is converted from a gas to a liquid. Moisture will condense on a cool surface if the temperature is at or below the dew point and this can occur on an interior slab if the building temperature/environment is not controlled. The moisture present can be enough to inhibit bond. To eliminate this potential, check the dew point. Do not coat if you are within 5 degrees of the dew point. If this is not possible, leave a fan running overnight in the room to be coated.
Moisture Vapor Transmission
Coatings are the most likely resinous floor system to fail when excessive vapor is being transmitted from the concrete. Use a calcium chloride test kit to verify the transmission rate before coating. If readings are above the acceptable limits, contact your coating supplier’s technical service department. If you are not familiar with these test kits, how to use them or what they mean, contact your coating supplier’s technical service department.
Mixing
Drill speeds and paddle should match the volume to be mixed. The spiral type paddle works very well with coatings. Avoid a vortex due to paddle size or drill speed; this will whip air into the coating. Do not “pump” the paddle up and down. Quantities less than a gallon can be mixed by hand. In pigmented systems, and as a general practice, it is a good idea to measure off the curing agent/hardener and put into the mixing container first. These materials are typically lower in viscosity and weight per gallon than the surface refining agent. They are very good wetting agents. As you add the surface refining agent, it will displace the curing agent/hardener, which will come to the top, coating the bottom and sides. The drill and paddle will now not have to remove the sticky refining agent from the sides and bottom of the bucket.
When you mix an epoxy you start a chemical reaction that is accelerated in mass. Mix no more than can be applied in 30 minutes. Once mixed, dump the entire quantity on the floor. Product left in the bucket for several minutes will be at a different stage of cure than material first placed. This can affect flow, texture, air release and pigment float. The higher the viscosity of the material being mixed, the longer you mix. For an epoxy to cure fully, each molecule of hardener must find the appropriate molecules of epoxy resin to react. As more and more connections occur, the remaining molecules have more difficulty finding each other.
Priming
Good primers penetrate the substrate and provide a good bond site for the next application. They also reduce concrete out-gassing and provide some film build to reduce surface profile. Match your primer to the coating system. Most manufacturers make several primers for different conditions: low temperature, oily substrates, solvent or 100% solids, blush resistant, etc. As a general rule, use the fastest curing, low viscosity primer available. This combination works best to reduce out-gassing from the substrate.
Application
As a general guideline, do not exceed 20 milliliters of “neat” resin per lift without the use of a filler. Most formulations work best at 8-12 milliliters. Thick films will be more brittle and have a tendency to hold more air bubbles. Without exception, the best results will come from applying the product with a flat squeegee and back rolling with a high quality short nap roller. A squeegee distributes the material evenly and is the most efficient in terms of time. It also insures the entire mix is curing at the same rate. If you cannot use a squeegee, pour the entire mix in a ribbon and roll in and out of the ribbon. Keep the roller fully wet, otherwise it will fill with air, which can end up as bubbles in the coating.
Recoat Window
Follow the guidelines listed on the technical data sheet for the primer, fill resin or topcoat. Recoat windows will be impacted by temperature. A recoat window of 24 hours at 70 Fahrenheit will be reduced by several hours if installation temperatures were above 80. If in doubt, or you are at or beyond the recoat window, sand prior to coating. Do not recoat a solvent-based primer until the solvent has evaporated.