
SPARC of Ingenuity
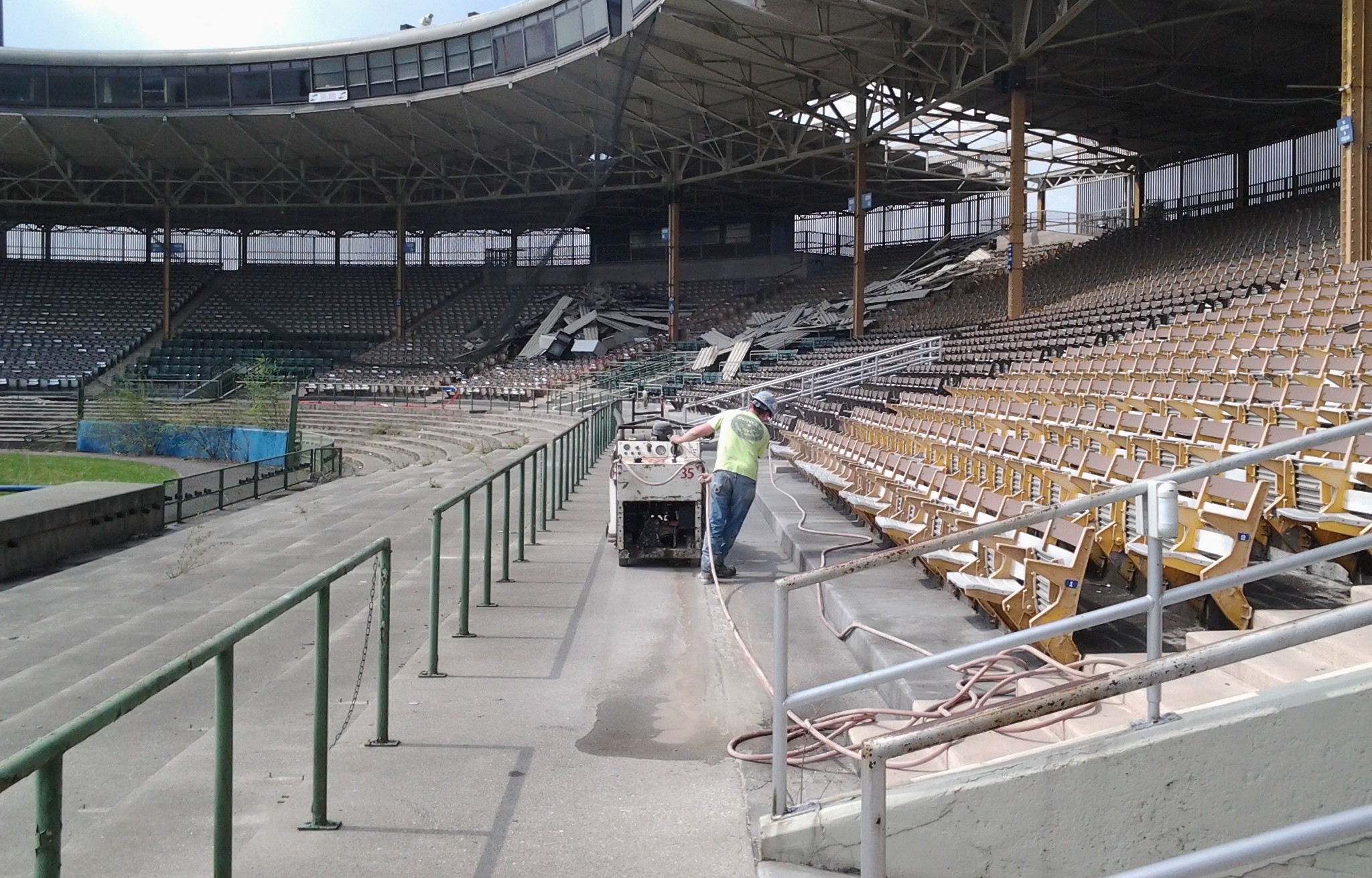
Diamonds Key to Baseball Stadium Transformation

Concrete flat saws were used to cut the 12-inch-thick landing slab around the stadium’s grandstands.
The crack of the bat and the roar of the home crowd at Cooper Stadium may have faded, but soon the roar of engines and the smell of gasoline will fill the Columbus, Ohio venue. A $40-million project is underway to transform the former home of Minor League Baseball’s Columbus Clippers into a state-of-the-art racetrack and automotive research and training center. For three months this year, however, the only noises heard inside the stadium were made by a cutting contractor helping to remove approximately 6.75 million pounds of concrete.
The 15,000-capacity Cooper Stadium was closed in 2008 and left vacant until this year, when work began to convert it into the 8,500-seater Sports Pavilion and Automotive Research Center (SPARC). The new center will include a half-mile paved oval track, a technology center, lodging facilities, a conference center and exhibition space. To realize this plan, the existing grandstands of the derelict stadium had to be renovated and structures like dugouts, seating areas, light poles, press boxes, roof coverings and steel supports had to be removed.
Given the rich history of the stadium, it was exciting to be a part of the renovation process. Not only did we get to work on a historical venue, we also got to work on what will be a one-of-a-kind facility
-Jason Young, operations manager for Donley Concrete Cutting Co. of Pickerington, Ohio, a local CSDA member chosen by general contractor Loewendick Demolition Contractors, Inc. of Grove City, Ohio, for concrete sawing tasks in several parts of the stadium.
It was determined that concrete sawing with diamond tools was the only feasible option to safely separate the concrete grandstands. Once the specified sections were cut, traditional demolition tools like jackhammers and wrecking balls were used to break them down. The precision and accuracy of the concrete sawing techniques meant the sections could be demolished in isolation without compromising the structural integrity of adjacent sections that were to remain. In addition, the method of sawing with diamond blades provided clean, finished edges that would benefit the construction of the new pavilion—not to mention the saws could be set up in areas with limited access that were unreachable by larger demolition equipment.
First, Donley Concrete Cutting set up on the 245-foot-long, 8-foot-wide and 12-inch-thick concrete landing slab and used a Diamond Products CC 6500 flat saw fitted with a 30” diameter blade to make the cuts. The landing was divided into 12 sections that were broken out after cutting. Further cuts were required to separate the landing slab from the grandstands. For these areas, which could not be cut by the flat saw, a customized Husqvarna K2500 hydraulic hand saw was used to make flush cuts. Power came from a Diamond Products truck-mounted unit, which supplied 480-volt electric power to a CB40 EXL portable hydraulic power unit. This portion of the cutting work took around 14 hours to complete.

Customized flush cut hand saws were used in areas where flat sawing equipment could not be placed.
Operators again utilized the flush cut hand saw, along with an ICS 890F4 chain saw, to cut along the perimeter of the upper grandstand mezzanine slab. These cuts separated the mezzanine slabs, walls and ramps in preparation for cutting the grandstand risers. Operators cut four separate areas of the grandstand mezzanine to an average depth of 6 inches. Some blades became stuck while cutting because of structural shifts, so shoring was placed below the cutting areas to eliminate these shifts.
Treads and risers were cut by an operator using a Diamond Products CC1600 wall saw capable of both regular and flush cutting capabilities. Cuts were made from the top to the bottom of each riser, which allowed the general contractor to demolish and remove the specified grandstand sections. The steps on the risers were 9 inches tall, 36 inches wide and 12 inches deep. The average thickness of the steps was 12 inches and there were around 30 steps per riser. Operators were able to cut the entire elevation of one riser in eight hours, making one continuous cut from top to bottom.
To complete the required cutting work, Donley Concrete Cutting operators returned to the lower grandstand areas and used the wall and chain saw to cut supporting concrete beams. These 36-inch-tall by 14-inch-thick beams supported the landing slab and could not be accessed until the general contractor broke out the cut slab sections. While cutting the slab, however, operators had layouts to identify where the beams were located and made deeper cuts to penetrate the top of the beam. This allowed the layout to be transferred after the slab sections had been removed and the beams were exposed. A total of 11 beams were cut, taking 12 hours to complete.
On the surface, the prospect of working in an open stadium structure would seem to be easier than other, less spacious jobsites, but the issue of stair-only access to both the upper and lower work areas did restrict the contractor in terms of sawing options. Also, ongoing demolition work being performed by other contractors during the cutting work presented further limitations. Portable hydraulic generators, water supplies and sawing equipment were all craned into each work area, allowing the majority of the work to be completed without the need for a truck.

Operators also cut support beams that were exposed after demolition of the slab.
Donley Concrete Cutting worked on the jobsite for two weeks to complete the necessary sawing required for the demolition work. The general contractor went on to remove 6,750,000 pounds of concrete and approximately 6,500 seats from the old stadium. The project was completed both on time and within the estimated budget.
“We were awarded the project based on our reputation to manage projects in a timely manner with highly trained operators. Completing jobs safely and within budget is always our priority, so this was no different,” explained Young.
At present, SPARC Ohio is due to open in 2015. The capabilities of concrete sawing equipment has provided the owners with a way to renovate and build around existing structures at the former Cooper Stadium, saving them both time and money.
Cooper Stadium
The 47-acre site, which was anchored by the 15,000 seat stadium, originally was constructed for $450,000. The $40-million renovation will reduce the capacity of the stadium to 8,500 around a newly-constructed half-mile racetrack. The overall site will include a 50,000-square-foot automotive research center as well as lodging facilities, a conference center and exhibition space. When complete, the venue will host such events as auto racing, motocross, cycling, auto shows as well as concerts and festivals. Along with a partnership with select businesses and educational institutions, the facility will also be used as a test site for automotive engineers and technicians as well as a venue for driver training, consumer education and sales.
Company Profile
Donley Concrete Cutting Co. has been a CSDA member since 2004 and is based in Pickerington, Ohio, with a support location in Cincinnati. The company has been in business for 17 years. It has 50 employees, 40 trucks and offers the services of core drilling, wall sawing, wire sawing, flat sawing, curb sawing, diamond grooving and grinding, profilograph services, selective demolition and ground penetrating radar.
Resources
General Contractor:
Loewendick Demolition Contractors, Inc.
Sawing and Drilling Contractor:
Donley Concrete Cutting Co.
Pickerington, Ohio
Phone: 614-834-0300
Email: Jason.young@donleyconcrete.com
Website: www.donleyconcrete.com
Methods Used: Flat Sawing, Wall Sawing, Hand Sawing