
Towering Success
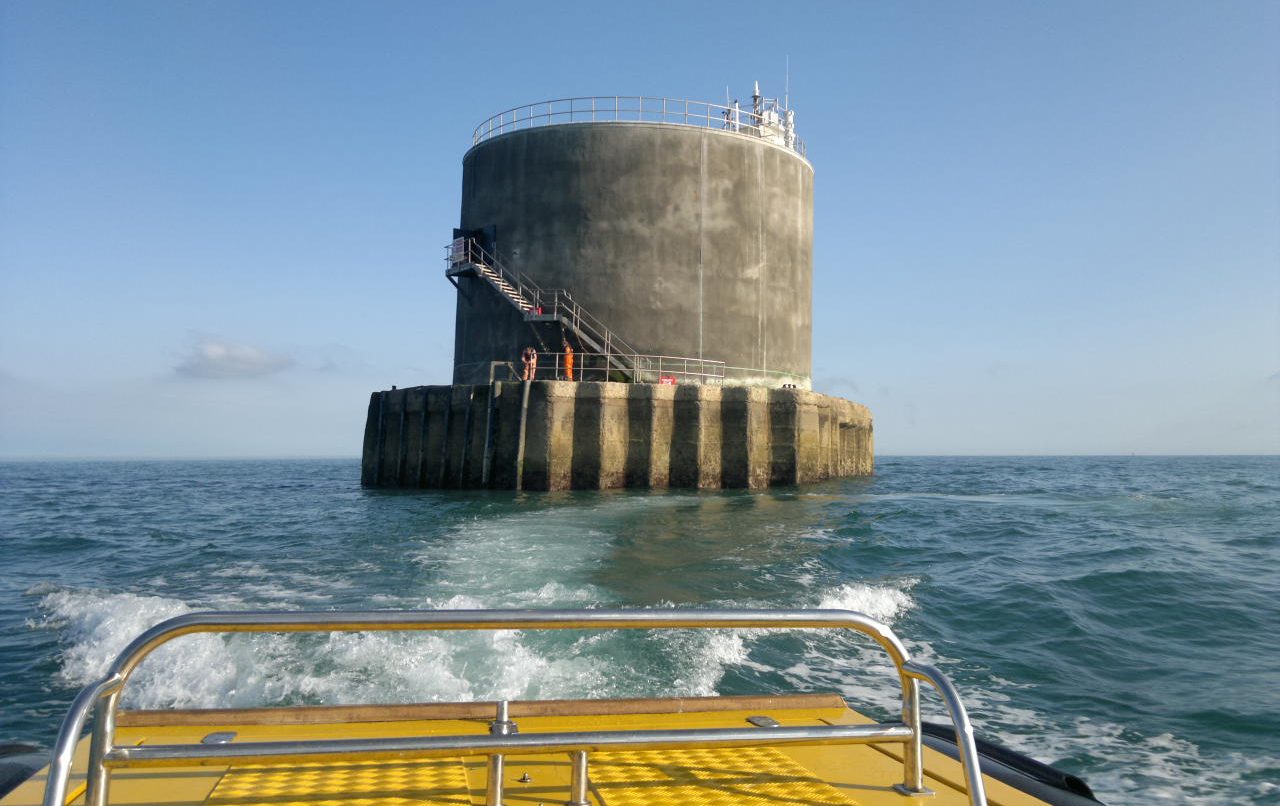
Lighthouse Refurbished Using Diamond Tools
A major refurbishment of a century-old lighthouse tower off the southern coast of England was completed with help from a professional core drilling contractor.
The overall project involved reducing the tower to half its original height above the water, from 22 to 11 meters (72.2 to 36.1 feet), with additional tasks required to create openings in the concrete wall and upper deck of the structure.

Nab Tower was halved in height to 11 meters (36.1 feet) as part of extensive refurbishment work.
Nab Tower was originally constructed as a defensive structure during World War I, but only became operational in 1920 after the conflict had ended. The tower is positioned in the Solent, a 20-mile passage of water that separates the Isle of Wight from the English port cities of Portsmouth and Southampton, and was used during World War II to repel enemy aircraft and sea vessels crossing the English Channel from mainland Europe.
Since then the structure has been used as a lighthouse. It became unmanned in 1983 and a 2013 survey found extensive deterioration to the concrete and steelwork, rendering the tower unsafe to land helicopters on its landing pad. Trinity House, a charity dedicated to safeguarding shipping and seafarers, put a plan in motion to refurbish Nab Tower and secure its future for another 50 years.
The charity appointed general contractor BAM Nuttall of Camberley, England for the work. As work progressed, the company set about finding a specialist concrete cutter to complete some of the refurbishment tasks. The Alton office of CSDA member D-Drill Master Drillers Ltd. was contracted to do the work, which involved the drilling of 46 holes for the installation of ventilation ducts through the concrete wall and upper deck of the lighthouse.
“The complication here was not the holes we had to drill, but the access to the location and the fact that we had to get everything over to Nab Tower and off again in a single day—including drills, generators, the men and their lunch,” said John Barber, D-Drill branch manager. “The job was twice rescheduled due to poor weather conditions. Working ten nautical miles from shore in water that was 20 meters (65.6 feet) deep, everyone had to be absolutely certain that the operators and equipment could be safely transported to and from the tower and that the weather conditions would be calm enough to complete the work.”
Dean Gough and Liam Berry, operators from D-Drill’s Alton office, were taken by boat across the Solent to Nab Tower on July 2, 2015 to perform core drilling techniques. The operators were equipped with two Hilti DD350 core drill rigs, two 110-volt gas-powered generators and all required equipment, which had to be manually lifted across to the tower after docking.

Diamond core bits were used to create four 200-millimeter-diameter (7.9-inch) holes in the tower’s concrete helipad slab.
The core drilling work began with the creation of four holes measuring 200 millimeters (7.9 inches) in diameter to a depth of 400 millimeters (15.7 inches) in the concrete slab next to the helicopter landing area. The holes were positioned approximately 5 meters (16.4 feet) apart and 600 millimeters (23.6 inches) from the edge of the platform. Each hole took around one hour to complete, including the secure mounting and removal of the drill rig.
Next, operators mounted the core drill rigs on a vertical wall and used stitch drilling techniques to form an opening 250 millimeters (9.8 inches) tall by 210 millimeters (8.3 inches) wide through 300 millimeters (11.8 inches) of concrete that was also for the ventilation duct work. A 107-millimeter-diameter (4.2-inch) bit was employed to make six penetrations and create the required opening, taking approximately two hours to complete. A further 36 140-millimeter-diameter (5.5-inch) fixing holes were drilled around the tower for the installation of steel support work.
Working a 16-hour shift, Gough and Berry ensured that each of the 46 holes required at Nab Tower were completed in one day, much to the satisfaction of the general contractor. Had the core drilling team failed to achieve this, extra time and money would have been spent scheduling and executing a repeat visit.
“Of course, we had to follow very strict health and safety procedures on the job, wearing life jackets at all times. It was important to the customer to get the work done, but there was to be no compromises when it came to safety—hence the job was twice postponed because of the inclement weather conditions,” added Barber. “Our team always looks forward to a challenge and the Nab Tower job very much provided that. It is yet another example of how we work on a whole range of conditions and environments—always ensuring we get the job done.”

Stitch drilling techniques were used to create the specified openings.
D-Drill’s work at Nab Tower was completed in one day, as contracted. The refurbished structure now has new layers of concrete, new Automatic Identification System and radar beacons and a new fixed main light with a range of 12 nautical miles. The installation of updated ventilation ducts was completed on schedule.
A spokesperson for BAM Nuttall, Jonathon Pitt, said: “The Nab Tower refurbishment was a very challenging project, taking two-and-a-half years to complete due to the weather dictating our daily ‘commute’. We needed a local, reliable diamond driller with operators who didn’t mind getting their feet wet and D-Drill delivered.”
Company Profile
D-Drill Master Drillers Ltd. has been a member of CSDA for 34 years and has been in business since 1967. Based in Coventry, England, the company has 94 employees and 70 trucks in 10 locations across the country. D-Drill offers services that include core drilling, slab sawing, wall sawing, hand sawing, wire sawing, controlled demolition, diamond floor grinding and floor preparation services.
Resources
General Contractor:
BAM Nuttall
Sawing and Drilling Contractor:
D-Drill Master Drillers Ltd.
Coventry, United Kingdom
Phone: 44-1752 341364
Email: johnbarber@d-drill.co.uk
Website: www.d-drill.co.uk
Methods Used: Core Drilling